Automobile manufacturing: A model of industrial excellence in the era of Industry 4.0.
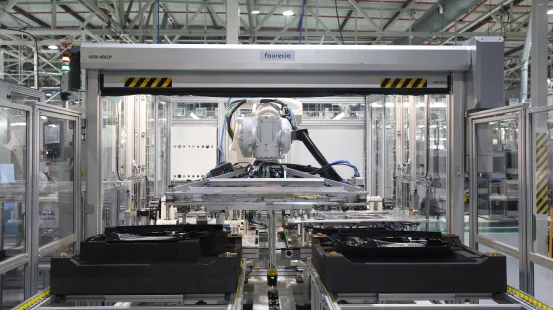
The automotive industry has always been a driving force of innovation and a model of industrial excellence. From scientific work organization to lean manufacturing, it has shaped major production methods and integrated cutting-edge technologies such as automation and robotics. Today, in the era of Industry 4.0, it faces unprecedented challenges: digitalization, increased flexibility, environmental requirements, and the shift toward software-defined vehicles. In this rapidly evolving landscape, FORVIA exemplifies how the automotive industry continues to push the boundaries of performance and sustainability.
The automotive industry has always been a fertile ground for technological innovation and a pioneer among manufacturing industries.
This is evidenced by the key industrial production concepts defined in the 20th century. Fordism, developed by Henry Ford as an extension of Taylorist principles of scientific management to enhance productivity in automotive manufacturing, was quickly adopted across industries. Similarly, Toyota’s toyotism, designed to boost productivity while improving quality and reducing costs, led to lean manufacturing, a method now used in many sectors.
The automotive industry also pioneered automated manufacturing: in 2023, it had the highest number of robots worldwide, with one million units—about one-third of all robots used across industries[1].
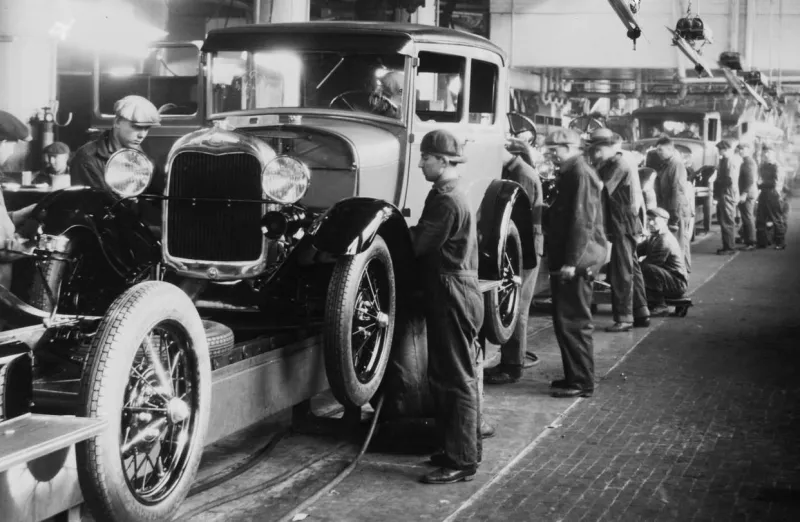
A high-precision industry with unparalleled complexity
The automotive sector stands as a trailblazer because it operates in an ecosystem of unmatched complexity applied to high production volumes.
A car is unlike any other manufactured object. It is a combination of systems that have grown more intricate over time with technological advancements, evolving from purely mechanical (“hardware”) systems to integrated electronic (“hardware + software”) solutions. Today’s vehicle is an ultra-sophisticated entity, built from highly diverse modules that require mastery of numerous industrial processes, embodying high-precision electromechanics.
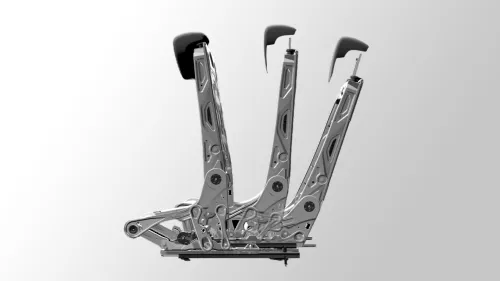
Take, for example, the production lines at FORVIA’s Seating plant in Wuxi, China: the small seat joints manufactured there feature gear teeth stamped with micron-level precision by massive presses, ensuring smooth and silent seat adjustments. Similarly, at the Interiors plant in Hénin-Beaumont, France, which specializes in plastics manufacturing, hundreds of components like consoles and dashboards are produced daily. Enormous presses, ranging from 600 to 2,700 kg, inject plastic materials—many of them bio-based and recycled, such as NAFILean-R (a blend of hemp fibers and recycled plastic)—into complex, digitally machined molds that are polished to perfection for a flawless finish.
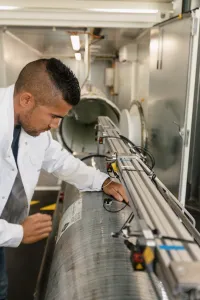
Automotive systems must meet multiple and sometimes conflicting technical requirements: safety and comfort, strength and lightness, durability and cost control, all while ensuring high-quality production at large volumes. At the Clean Mobility plant in Allenjoie, France, mass-produced hydrogen storage tanks undergo pressures of 1,575 bar—1,575 times atmospheric pressure, over twice their normal operating pressure. This is equivalent to the pressure experienced at a depth of 15,000 meters underwater, a challenge these tanks must withstand to enable trucks and buses to achieve ranges of several hundred kilometers.
Adding to this complexity is the industry’s reliance on a highly responsive market, demanding a supply chain that is both agile and finely tuned. The production process must be flexible and efficient enough to meet demand at any moment. This is the essence of the "Just-in-Time" (JIT) concept[2] and pull flow systems, pioneered and implemented by Toyota. In the automotive industry, factories process and produce orders in real time, allowing them to adapt to market fluctuations (volume, model variations, etc.) with minimal stock.
A single plant must manage production lines tailored to meet customers’ specific needs. For a given vehicle model, numerous seat options exist, differing in material, stitching, and comfort features like massage or heating. At FORVIA’s Seating plant in Allenjoie, four vehicle models are currently in production, amounting to nearly 200 different seat references. The technical challenge is immense, especially in a market with increasing volatility.
A showcase of operational excellence undergoing its greatest transformation
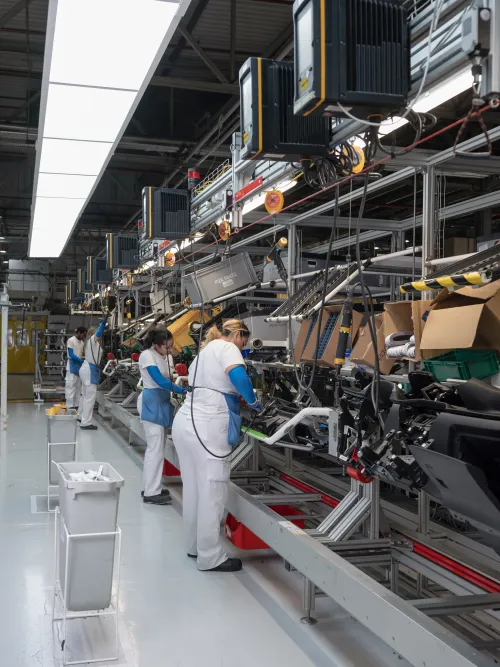
In automotive production, every task is optimized, and operational excellence is paramount. From the sequence of a hundred steps required to assemble a single component to the structuring of operator breaks, every detail follows a precise process. The industry cannot afford disruptions or errors—its long-term competitiveness depends on it, as does the safety of consumers and employees.
This is the foundation of the FORVIA Excellence System (FES), a comprehensive framework designed to help the group achieve excellence in safety, quality, and operational performance while ensuring total customer satisfaction. Incorporating best practices from Faurecia, HELLA, and other renowned industrial players, FES also supports teams in developing roadmaps for digitalization and sustainability. It is built to guarantee performance and continuous improvement, a strength that has earned FORVIA frequent recognition from its clients. Recently, five FORVIA plants received the prestigious General Motors Supplier Quality Excellence Award for exceeding the automaker’s strict quality performance criteria.
This drive for industrial excellence is all the more critical as the industry undergoes its most significant transformation since the invention of the combustion engine. The automotive sector must decarbonize—exploring new technologies, training workers in emerging skills—while evolving its industrial model to face growing global competition. Today, automakers, influenced by new American and Chinese entrants in the electric vehicle market, are increasingly drawing inspiration from the consumer electronics industry. This shift includes moving away from traditional model-based production in favor of assembling pre-existing modules and separating software development from hardware design. The concept of Software-Defined Vehicles (SDV) is now taking hold, with software becoming the central element around which vehicles are developed, allowing for continuous updates throughout their lifespan.
The challenge is to integrate this growing flexibility into the production chain while maintaining the highest quality standards.
A longstanding pioneer at the forefront of the sustainable 4.0 transition
It’s no coincidence that the automotive industry is now a driving force behind the Fourth Industrial Revolution, profoundly transforming its sector on a global scale.
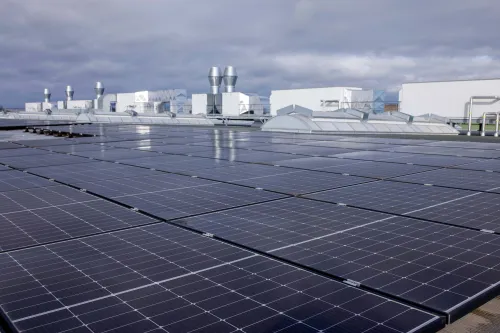
FORVIA plays a key role in the transition to Industry 4.0, firmly aligning it with decarbonization and sustainable development. The Group is the first company in the automotive sector to have its Net-Zero roadmap validated by the Science Based Targets initiative (SBTi). FORVIA is committed to achieving net-zero CO₂ emissions across its entire value chain by 2045, with two intermediate milestones: net-zero emissions for scopes 1 and 2 by 2025 and a 45% reduction in scope 3 emissions by 2030. To meet these ambitious goals while navigating the complexities of its ecosystem, the digitalization of its factories is a strategic priority. Among its 260 sites across 40 countries, FORVIA already operates over 100 model factories that leverage the latest digital tools and processes to achieve a high level of automation—automated guided vehicles, smart warehouses, data analytics, and 3D simulations to optimize operations.
A pilot site for FORVIA’s Interiors 4.0 program, the Tarazona plant in Spain has made a breakthrough in performance by implementing end-to-end automation of material flows, predictive production analysis through highly digitalized data tracking in manufacturing and supply chains, and green initiatives to fully decarbonize its operations. This model is already inspiring factories in Gorzów, Poland, and Spring Hill, USA.
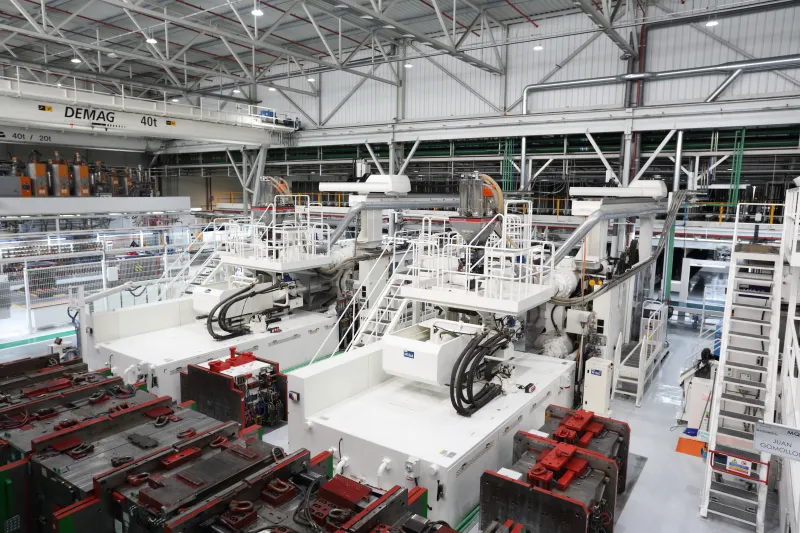
Another showcase of FORVIA’s innovation, the Seating plant in Allenjoie is one of the most technologically advanced in the world. This JAT 4.0 factory can produce seat kits with unprecedented production flexibility, closely aligned with customer needs, thanks to three key innovations:
- Automated component and finished product storage management, which enhances traceability throughout the manufacturing process while optimizing storage space.
- Fully digitalized plant control, enabling real-time monitoring of production flows, product quality, and machine performance, ensuring maximum responsiveness to disruptions and customer demands.
- A fleet of 300 autonomous mobile robots (AGVs), precisely calibrated to the centimeter, transporting components and finished products throughout the factory without human intervention—reducing delivery times and improving operator safety.
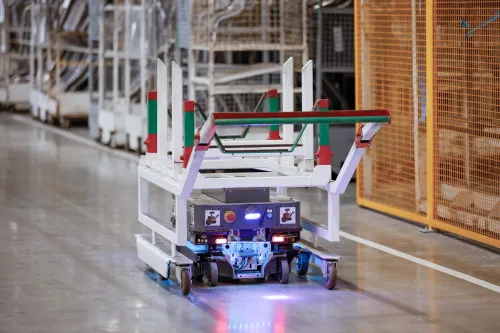
Within the industrial platform it shares with the Clean Mobility plant, the Allenjoie Seating facility is also at the forefront of sustainable production. Both production units have received BREEAM Excellent certification—a first for an industrial site in France.
FORVIA is also innovating in China with its new Fengcheng electronics mega-plant, its first carbon-neutral factory and one of the first in the world designed at such a scale using digital twin technology. Even before construction began, the operations of its 89 production lines and supply chain, fully integrating AI, digitalization, and automation, were simulated in a digital model. This innovative approach streamlined the construction process, shortening project timelines while enhancing both energy efficiency and operational performance.
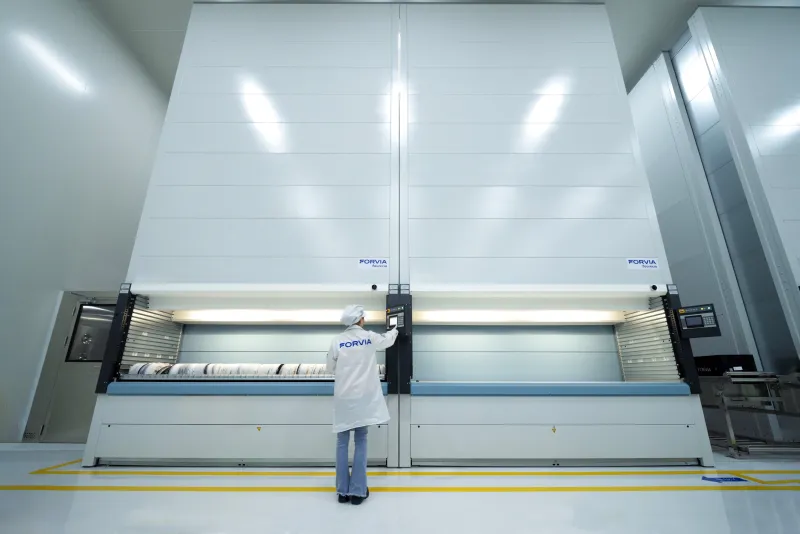
A dynamic industry offering an exciting playing field for its teams
It’s clear: working at an automotive production site is a daily challenge, but also a unique opportunity to be at the heart of an industry undergoing a major transformation.
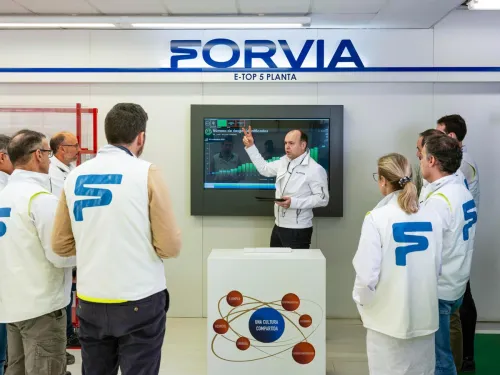
This is where the majority of our workforce is based and where a significant part of our success is built, day after day. If you have a passion for hands-on work and teamwork, a taste for challenges and problem-solving—because that’s the daily reality for our operational teams, who never have a dull moment!—you will find an opportunity to embark on a unique human adventure, gaining humility, agility, and leadership skills every day.
This experience is all the more enriching as it allows exposure to a wide range of professions, both technical (HSE, maintenance, quality, program launches) and managerial (supervision, plant management, operations leadership, HR). It also fosters close collaboration with multiple corporate functions (R&D, sustainability, finance, HR, strategy, projects...)—a level of integration not always found in more segmented industries—offering a rare springboard for career growth in a globalized group. At 25, in an automotive supplier like FORVIA, you can already be responsible for a production unit and manage dozens of people.
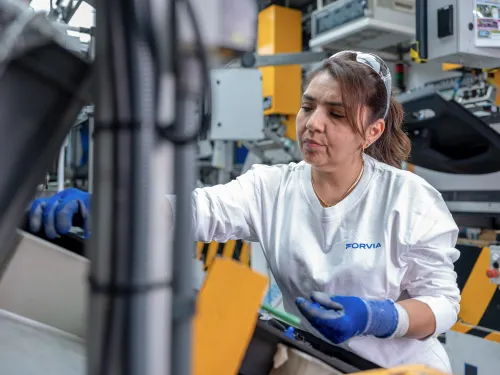
By joining our teams on the ground, you will experience firsthand the digitalization of operations shaping the industry of the future and contribute to the "butterfly effect" (the Blue Effect at FORVIA), where every daily action—from waste management to biodiversity preservation—plays a role in protecting the planet. You will also be at the forefront of learning the jobs of tomorrow and building future industries. At FORVIA, the workforce at the Clean Mobility plant in Allenjoie was the first to train through the H2 School academy, transitioning from the Group’s historical expertise in emissions control to the mass production of onboard hydrogen storage systems—a technology in which FORVIA is a pioneer.
Do you see yourself in our projects? What could be more inspiring than giving meaning to your work by becoming an active player in the energy transition and the future of sustainable mobility?
[1] See International Federation of Robotics (IFR), “World Robotics R&D Programs,” January 2023.
[2] A just-in-time (JIT) factory aims to minimize product lead time through various production stages, as well as work-in-progress and inventory levels.